Los últimos dos años (2015 y 2016) pueden considerarse como el momento crítico de la impresión directa en metal (DMP) en la industria aeroespacial, ya que la tecnología no dejó de cambiar: desde prototipos a piezas de producción y ensamblajes listos para despegar.
Durante ese período, Airbus Defence and Space trabajó junto a 3D Systems para lograr el mayor avance: el primer filtro de radiofrecuencia (RF) impreso en 3D, probado y validado para el uso en satélites de telecomunicaciones comerciales. El proyecto se basa en la investigación financiada por la Agencia Espacial Europea (A0/1-6776/11/NL/GLC: Modelling and Design of Optimised Waveguide Components Utilising 3D Manufacturing Techniques [Modelado y diseño de componentes optimizados para guías de ondas con técnicas de fabricación en 3D]).
Los filtros metálicos de radiofrecuencia o guías de ondas se remontan a los primeros sistemas de comunicaciones espaciales, hace casi 50 años. Los filtros funcionan como policías de tránsito: permiten que las frecuencias de determinados canales pasen y rechazan aquellas de señales que provienen de fuera de dichos canales.
Una tendencia de la industria es aumentar la capacidad de múltiples rayos dentro de un solo satélite. Un satélite de alta capacidad como el Eutelstat KA-SAT fabricado por Airbus Defence and Space lleva alrededor de 500 filtros de radiofrecuencia y más de 600 guías de ondas. Muchos de estos se diseñan de forma personalizada para tratar frecuencias específicas.
Cumplimiento de mandatos críticos
Los satélites de telecomunicaciones son un ejemplo del énfasis constante de la industria aeroespacial en reducir el peso, ya que enviar un vehículo a una órbita geoestacionaria puede costar hasta 20 000 USD por kilogramo. Continuar innovando respecto del diseño y reducir el tiempo de producción también son prioridades importantes, ya que la mayoría de los satélites están diseñados para tener una vida útil de entre 10 y 15 años.
Estas prioridades hacen que los satélites de telecomunicaciones sean ideales para la impresión directa en metal. La impresora ProX® DMP 320 de 3D Systems utilizada en el proyecto de filtros de radiofrecuencia para Airbus permite que los fabricantes consoliden piezas, mejoren la funcionalidad con formas y superficies que no serían posibles de realizar mediante los métodos de fabricación tradicionales, reduzcan el tiempo de producción y los costos para obtener diseños personalizados, y disminuyan el peso mientras se mantiene y mejora la resistencia del material.
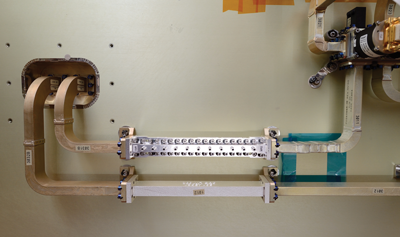
Nueva aplicación para una impresora probada
En las instalaciones de 3D Systems en Lovaina, Bélgica, se usó la ProX DMP 320 de 3D Systems desde que la máquina estaba en su etapa beta. Algunos proyectos exitosos incluyen la consolidación de piezas, la optimización topológica y la reducción de peso para piezas validadas en vuelos espaciales, como soportes y terminales puntales para satélites de telecomunicaciones. El proyecto Airbus Defence and Space fue la primera incursión de 3D Systems de Lovaina en filtros de radiofrecuencia.
La ProX DMP 320 está diseñada para ofrecer precisión y rendimiento altos en entornos de producción exigentes las 24 horas del día, los 7 días de la semana. Su amplia gama de aleaciones de LaserForm (titanio, acero inoxidable, aluminio, como-cobalto y cromo-níquel) está formulada y ajustada para esta impresora de metal a fin de que ofrezca piezas de alta calidad y propiedades uniformes.
Los modelos de fabricación intercambiables ofrecen una mejor versatilidad para las aplicaciones y menor tiempo de inactividad en el momento de cambiar entre diversos materiales de las piezas. Una cámara de vacío controlado garantiza que cada pieza se imprima con la pureza química, la densidad y las propiedades comprobadas del material.
Innovación revolucionaria del diseño
El proyecto de filtros de radiofrecuencia para Airbus Defence and Space demuestra la capacidad de la impresión en 3D a fin de permitir crear nuevos diseños para piezas aeroespaciales que no han tenido grandes cambios en décadas.
De forma tradicional, los filtros de radiofrecuencia están diseñados según bibliotecas de elementos estandarizados, como cavidades rectangulares y secciones transversales de guías de ondas con curvas perpendiculares. Las formas y las conexiones se determinan según los procesos habituales de fabricación, como el fresado y la electroerosión. Como resultado, suele ser necesario mecanizar las cavidades de los filtros de radiofrecuencia a partir de dos mitades unidas. Esto aumenta el peso, agrega una etapa de ensamblaje al tiempo de producción y requiere
una evaluación de calidad adicional.
Diseñar las piezas de impresión 3D permitió que Airbus Defence and Space desarrollara geometrías complejas sin ningún costo de fabricación adicional.
Se utilizó la CST MWS, una herramienta estándar de software de simulación electromagnética en 3D, para diseñar los filtros de radiofrecuencia impresos en 3D, en los que se destinó poco tiempo a la optimización. Esta mayor flexibilidad en la fabricación gracias a la impresión en 3D posibilitó la obtención de un diseño mediante una cavidad superelipsoidal deprimida. Esta forma única permitió canalizar corrientes de radiofrecuencia y ofrecer las compensaciones necesarias entre el factor Q (una medida de eficiencia de guía de ondas según la pérdida de energía) y el rechazo de
señales fuera de banda.
“La innovación revolucionaria surge de que, ahora, cómo se diseñará el hardware se determina a partir de la funcionalidad pura y no de la capacidad de fabricación”, dice Koen Huybrechts, ingeniero de proyecto para 3D Systems en Lovaina. “Este proyecto es un ejemplo clásico de lo que se conoce como 'la forma sigue a la función'”.
“Los principales beneficios del diseño monolítico que permite la impresión en 3D son la masa, el costo y el tiempo”, expresa Paul Booth, ingeniero de radiofrecuencias en Airbus Defence and Space, en Stevenage, Reino Unido. “La masa se reduce debido a que ya no hay necesidad de contar con sujetadores. Además, con la impresión directa en metal existe la ventaja, sin costo, de que el perfil exterior siga más de cerca el perfil interno, por lo que solo se usa el metal realmente necesario. El beneficio de costo y tiempo surge al reducir el ensamblaje y el postprocesamiento”.
Eliminación de los problemas de la superficie
Al comienzo, se pensó que la topología diferente de las superficies en las piezas metálicas impresas en 3D serían un inconveniente, pero las exhaustivas pruebas de Airbus Defence and Space quitaron esos problemas.
“La topología microscópica es diferente en la pieza impresa en 3D que en una pieza mecanizada”, dice Booth. “Las superficies mecanizadas tienen picos y depresiones afiladas, mientras que las superficies impresas en 3D están hechas de esferoides fundidos, por lo que hay menos áreas filosas”.
“La forma esférica de las partículas de polvo usada en la impresión 3D en metal da lugar a determinada ondulación en lugar de tener transiciones pronunciadas”, expresa Huybrechts. ”Pero la posibilidad de darle forma a una pieza para obtener un filtro de señales más eficaz supera en demasía cualquier preocupación respecto de la topología de la superficie”.
“Estábamos muy contentos con el trabajo que 3D Systems hizo por nosotros y muchas personas en Airbus comentaron respecto de la buena calidad del acabado de la superficie”, dijo Booth. ”Realizamos algunas tomografías computadas por rayos X y nos sorprendimos con la densidad de la pieza y la calidad general de la superficie”.
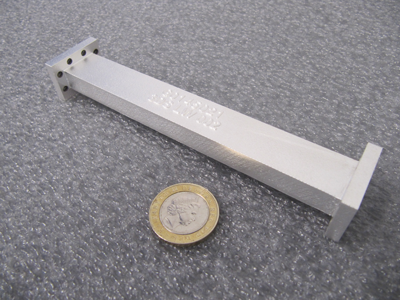
Pruebas rigurosas aprobadas
En sus instalaciones en Stevenage, Airbus Defence and Space probó tres muestras de aluminio impresas con la ProX DMP 320 mediante diferentes procesos. En las pruebas, imitaron las condiciones que las piezas enfrentarían durante el lanzamiento y en órbita, lo que incluye vibraciones, choques y situaciones térmicas como temperaturas extremas y condiciones de vacío. Las tres muestras cumplieron o superaron los requisitos. El mejor rendimiento tuvo lugar en un filtro enchapado en plata mediante un proceso electrolítico.
Más allá de la impresión en 3D, 3D Systems ofrece un valor agregado que es crucial para este tipo de proyectos, que incluye el tratamiento de polvo certificado, el control del proceso para una mayor densidad de materiales, el postprocesamiento probado y el control de calidad confiable.
Booth reconoce que esta experiencia agregada juega un papel importante en el éxito del proyecto: “Nos dimos cuenta de que no solo se trata de usar buenas máquinas para fabricar la pieza, sino que los buenos resultados también se deben a que 3D Systems comprende correctamente el proceso de fabricación”.
Importante potencial del retorno de la inversión
Ahora que el proceso se validó y que las piezas cumplen con los estándares más altos en vuelos espaciales de Airbus Defence and Space, la empresa puede comenzar a considerar el potencial retorno de la inversión de la impresión metálica en 3D. El proyecto ofreció el tipo de retorno de la inversión que entusiasma a un director financiero: tiempo de respuesta más rápido, menores costos de producción y una impresionante reducción del 50 % del peso.
Booth afirmó: “Se redujo la masa sin destinar nada de tiempo a la optimización y se puede reducir aún más con un diseño mecánico más agresivo. La reducción de la masa ahorra costos, ya que requiere menos propulsión en el cohete y menores demandas respecto de las estructuras de soporte, lo que permite reducir la masa aún más.
“El éxito de este proyecto abre la posibilidad de lograr una integración aún mayor de los filtros de radiofrecuencia con componentes mecánicos y térmicos para reducir la cantidad de piezas y la masa general. También estudiaremos la integración de más funcionalidades, como acopladores de prueba como parte del filtro o directamente integrados en las guías de ondas. Existe un gran potencial para reducir la masa a la vez que se reducen los costos y el tiempo de producción”.